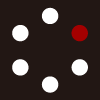
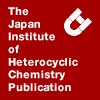
HETEROCYCLES
An International Journal for Reviews and Communications in Heterocyclic ChemistryWeb Edition ISSN: 1881-0942
Published online by The Japan Institute of Heterocyclic Chemistry
e-Journal
Full Text HTML
Received, 27th September, 2012, Accepted, 1st November, 2012, Published online, 14th November, 2012.
DOI: 10.3987/COM-12-S(N)125
■ Ligand Modified CuFe2O4 Nanoparticles as Magnetically Recoverable and Reusable Catalyst for Azide-Alkyne Click Condensation
Shingo Ishikawa, Reuben Hudson, Audrey Moores,* and Chao-Jun Li*
Department of Chemistry, McGill University, 801 Sherbrooke St. West, Montreal, Quebec H3A 2K6, Canada
Abstract
A ligand can make the trick: 2,2’-bipyridine was found to promote the activity of copper ferrite nanoparticles as catalysts for the azide-alkyne “click” coupling reaction. The reaction proceeded in excellent yields at room temperature, and the catalyst could be magnetically separated and recycled. Phosphorus and nitrogen containing ligands were tested and 2,2’-bipyridine proved to be the most efficient for this reaction.With nanoparticles (NPs) emerging as a powerful class of catalysts,1 there is a great need to develop means to ensure their recovery.2 One of the most promising strategies has been the use of magnetically recoverable NPs as recyclable catalysts and many organic transformations have already been developed.3 These systems allow an easy recovery in the presence of an external magnet, avoiding the need for centrifugation. Iron-based materials are particularly interesting as they combine magnetic properties with low toxicity and earth-abundance and they have proved effective catalysts for coupling,4 hydrogenation5 and oxidation reactions.6 Other simple magnetic NPs have allowed the scope expansion of such systems. Copper ferrite (CuFe2O4) NPs are inexpensive, air-stable, magnetically separable, and recyclable catalysts, which can catalyze C-C,7a C-N,7b C-O,7c C-S7d and C-Se7e cross-coupling reactions and other transformations.7f-7j
The azide-alkyne cycloaddition (AAC) reaction is a good illustration of these developments. The AAC8 is of great interest because this ‘click chemistry’ can rapidly create molecular diversity through the use of reactive modular building blocks.9 The catalyzed AAC reaction has found a wide range of applications in various research areas, including medicinal chemistry10 and material science.11 Typically the AAC reaction is catalyzed by Cu(I) salts; alternatively, Cu(II) may be used if coupled with a mild reducer such as sodium ascorbate.12 Cu(I) species may be immobilized onto polymers,13 zeolite,14 or magnetic nanoparticles to ease recovery.15 Heterogeneous systems have also been developed including Cu(0) on charcoal,16 Cu(0) NPs,17 microwave irradiated Cu turnings,18 and CuO nanostructures.19 Recently, we demonstrated that simple, unfunctionalized heterogeneous copper-plated iron NPs are effective catalysts for the AAC.20 This study was based on the rationale that the addition of Cu(II) salts to Fe(0) NPs provided the Cu(I) species necessary for AAC catalysis. In the course of this work, we attempted to achieve a similar outcome by adding sodium ascorbate to CuFe2O4 NPs to afford in situ reduction. Unfortunately, this resulted in the complete dissolution of the NPs, and thus prevented recovery. In the present work, we explored the addition of electron donating ligands to a Cu(II) containing material, CuFe2O4 NPs. This system provided a recoverable and very active catalyst for the AAC reaction.
Our initial studies began with the model cyclization of benzyl azide and phenyl acetylene using a catalytic amount of copper ferrite (Scheme 1). The coupling product was obtained in 15% NMR yield in the absence of ligand, however the reaction could be accelerated by heating up at 80 ˚C, providing the product in excellent yield as a single regioisomer.
In search of milder conditions, we sought to determine the best ligand for the nano-CuFe2O4-AAC reaction at room temperature. The results are summarized in table 1. The use of phosphine ligands led to increased yields (Table 1, entries 1 and 2). Trace amounts of product were obtained in the presence of acetylacetone (Table 1, entry 3). Monodentate nitrogen ligands such as pyridine did not significantly affect the reaction (Table 1, entries 4 and 5). Among the bidentate nitrogen ligands, TMEDA and 1,10 phenanthroline gave very poor results (Table 1, entries 6-7). 2,2’-Bipyridine derivatives gave the desired product in excellent yield (over 96%) (Table 1, entry 8). The amount of catalyst and ligand could be reduced to 5 mol% and surprisingly afforded 100% conversion. Tridentate ligands afforded only a trace amount of product (Table 1, entry 9). Control experiments were carried out to confirm that no product was obtained in the absence of copper catalyst (Table 1, entry 10). Likewise, entry 11 demonstrates the necessity of copper within the ferrite lattice, because replacing it with iron (Fe3O4) provides only a trace amount of product.
The influence of the solvent was evaluated under the optimized conditions. Diethyl ether, dimethyl sulfoxide (DMSO) and methanol afforded the products in moderate yields (Table 2, entries 4, 6 and 8). The reaction in water was possible in the presence of ligands, however, the nanoparticles dissolved and could not be recovered. Reactions conducted in ethyl acetate, acetone, toluene, THF and acetonitrile gave the product in excellent yield (Table 2, entries 1-3, 5 and 7). The reaction did not require strict conditions such as anhydrous (Table 2, entry 9) or degassed solvent or inert atmosphere – a noteworthy improvement over our previous report with copper plated iron(0) nanoparticles.20
With the optimized conditions in hand, we focused our attention to substrate generality. Various terminal alkynes including, aromatic and aliphatic acetylenes, were examined under these optimized conditions (Table 3). Aromatic alkynes with electron-withdrawing groups (Table 3, entries 4-6) were more reactive than those with electron-donating groups (Table 3, entries 2-3). Only a trace amount of product was obtained in the reaction with pyridylacetylene and most of the starting material was recovered. This is likely due to the strong coordination of the nitrogen in the acetylene, preventing activation of alkyne moiety. The reaction with an aliphatic alkyne was very sluggish. This reaction, therefore, required slight heating and a longer reaction time (Table 3, entry 11). The reaction with propargyl alcohol derivatives afforded the products in moderate to good yields (Table 3, entries 12-14). The reactions of primary, and secondary alkyl and functionalized azides with various alkynes are also effective to give the products in moderate yields (Table 3, entries 16-20).
To expand the utility of nano-CuFe2O4 for AAC, a reaction on a larger scale was carried out with 2 gram of substrates (Scheme 2). It should be noted that the click reaction successfully afforded the product in 96% yield and 90% of the catalyst was recovered (compared with Table 3, entry 18).
The reusability of the nano-CuFe2O4 catalyst was examined and the results are summarized in Figure 1. The reaction of benzyl azide with phenylacetylene was chosen as a model reaction. The catalyst was magnetically separated from the reaction mixture after completion of the reaction, washed with solvent and used directly for further AAC reaction. Acetonitrile, acetone, toluene, THF and ethyl acetate were
tested as solvents over 5 cycles. Ethyl acetate proved to be the best solvent with very little attrition of activity over 5 cycles (Figure 1, ESI). The catalyst loading was also tested in the recycling context. One or two mol% led to a decrease in activity over 5 cycles, while 5 or 10 mol% enabled the system to sustain catalytic activity.21
To check for potential leaching of metal into the solution, ICP-OES analysis was carried out. After the reaction, the nanoparticles were magnetically removed and the solution was filtered through Celite. The reaction at room temperature and 40 °C were tested (Table 3, entries 1 and 11). It was determined to be 0.027 and 0.45 ppm, respectively. This result strongly suggests a heterogeneous mechanism. Figure 1a, b in ESI shows the TEM images of the CuFe2O4 catalyst before and after use.
The reaction mechanism has not yet been elucidated, but on the basis of the previously reported Cu(II)-Hydrotalcite catalyst by Pitchumani and co-workers,22 we propose the mechanism described in Scheme 3. The reaction may proceed through an activation of alkyne, followed by cycloaddition of azide and protonation on the surface of the copper ferrite nanoparticles. The observation of the sole 1,4-adduct as reaction product is in agreement with the proposed mechanism.
In conclusion, we have demonstrated the application of CuFe2O4 nanoparticles for ‘click’ reaction. The reaction did not require strict conditions such as anhydrous or degassed solvent or inert atmosphere, and was applicable for gram scale synthesis. The catalyst could be separated and recovered easily by an external magnet and efficiently reused several times without significant loss of activity. Further applications of magnetic nanoparticles are in progress in our laboratory.
ACKNOWLEDGEMENTS
We thank the Natural Science and Engineering Research Council of Canada (NSERC), the Canada Foundation for Innovation (CFI), the Canada Research Chairs (CRC), the Fonds de Recherche sur la Nature et les Technologies (FQRNT), the Center for Green Chemistry and Catalysis (CGCC), the Green Chemistry - NSERC Collaborative Research and Training Experience (CREATE) Program and McGill University for their financial support.
References
1. a) D. Astruc, F. Lu, and J. R. Aranzaes, Angew Chem. Int. Ed., 2005, 44, 785; CrossRef b) V. Polshettiwar and R. S. Varma, Green Chem., 2010, 12, 743. CrossRef
2. D. J. Cole-Hamilton, Science, 2003, 299, 1702. CrossRef
3. a) S. Shylesh, V. Schünemann, and W. R. Thiel, Angew. Chem. Int. Ed., 2010, 49, 3428; CrossRef b) V. Polshettiwar, R. Luque, A. Fihri, H. Zhu, M. Bouhrara, and J.-M. Basset, Chem. Rev., 2011, 111, 3036; CrossRef c) T.-J. Yoon, W. Lee, Y.-S. Oh, and J.-K. Lee, New J. Chem., 2003, 27, 227; CrossRef d) A.-H. Lu, E. L. Salabas, and F. Schüth, Angew. Chem. Int. Ed., 2007, 46, 1222. CrossRef
4. a) R. B. Bedford, M. Betham, D. W. Bruce, S. A. Davis, R. M. Frost, and M. Hird, Chem. Commun., 2006, 1398; CrossRef b) T. Zhen, W.-W. Chen, C. M. Cirtiu, A. Moores, G. Song, and C.-J. Li, Green Chem., 2010, 12, 570. CrossRef
5. a) P.-H. Phua, L. Lefort, J. A. F. Boogers, M. Tristany, and J. G. de Vries, Chem. Commun., 2009, 3747; CrossRef b) R. Hudson, A. Rivière, C. M. Cirtiu, K. L. Luska, and A. Moores, Chem. Commun., 2012, 48, 3360. CrossRef
6. F. Shi, M. K. Tse, M.-M. Pohl, A. Brückner, S. Zhang, and M. Beller, Angew. Chem. Int. Ed., 2007, 119, 9022. CrossRef
7. a) N. Panda, A. K. Jena, and S. Mohapatra, Chem. Lett., 2011, 40, 956; CrossRef b) N. Panda, A. K. Jena, S. Mohapatra, and S. R. Rout, Tetrahedron Lett., 2011, 52, 1924; CrossRef c) R. Zhang, J. Liu, S. Wang, J. Niu, C. Xia, and W. Sun, ChemCatChem, 2011, 3, 146; CrossRef d) K. Swapna, S. N. Murthy, M. T. Jyothi, and Y. V. D. Nageswar, Org. Biomol. Chem., 2011, 9, 598; e) K. Swapna, S. N. Murthy, and Y. V. D. Nageswar, Eur. J. Org. Chem., 2011, 1940; CrossRef f) M. L. Kantam, J. Yadav, S. Laha, P. Srinivas, B. Sreedhar, and F. Figueras, J. Org. Chem., 2009, 74, 4608; CrossRef g) J. E. Tasca, A. Ponzinibbio, G. Diaz, R. D. Bravo, A. Lavat, and M. G. González, Top Catal, 2010, 53, 1087; CrossRef h) M. L. Kantam, J. Yadav, S. Laha, and S. Jha, Synlett, 2009, 1791; CrossRef i) B. Sreedhar, A. S. Kumar, and D. Yada, Tetrahedron Lett., 2011, 52, 3565; CrossRef j) B. S. P. A. Kumar, K. H. V. Reddy, B. Madhav, K. Ramesh, and Y. V. D. Nageswar, Tetrahedron Lett., 2012, 34, 4595. CrossRef
8. a) C. W. Tornøe, C. Christensen, and M. Meldal, J. Org. Chem., 2002, 67, 3057; CrossRef b) V. V. Rostovtsev, L. G. Green, V. V. Fokin, and K. B. Sharpless, Angew. Chem. Int. Ed., 2002, 41, 2596; reviews on the copper-catalyzed formation of triazoles; CrossRef c) V. D. Bock, H. Hiemstra, and J. H. van Maarseveen, Eur. J. Org. Chem., 2006, 51; CrossRef d) J. E. Moses and A. D. Moorhouse, Chem. Soc. Rev., 2007, 36, 1249; CrossRef e) M. V. Gil, M. J. Arévalo, and Ó. López, Synthesis, 2007, 11, 1589; CrossRef f) P. Wu and V. V. Fokin, Aldrichimica Acta, 2007, 40, 7.
9. a) H. C. Kolb, M. G. Finn, and K. B. Sharpless, Angew. Chem. Int. Ed., 2001, 40, 2004; CrossRef b) H. C. Kolb and K. B. Sharpless, Drug Discovery Today., 2003, 8, 1128; CrossRef c) M. Meldal and C. W. Tornøe, Chem. Rev., 2008, 108, 2952. CrossRef
10. a) W. G. Lewis, L. G. Green, F. Grynszpan, Z. Radić, P. R. Carlier, P. Taylor, M. G. Finn, and K. B. Sharpless, Angew. Chem. Int. Ed., 2002, 41, 1053; CrossRef b) N. J. Agard, J. A. Prescher, and C. R. Bertozzi, J. Am. Chem. Soc., 2004, 126, 15046; CrossRef c) A. Krasiński, Z. Radić, R. Manetsch, J. Raushel, P. Taylor, K. B. Sharpless, and H. C. Kolb, J. Am. Chem. Soc., 2005, 127, 6686; CrossRef d) J. M. Baskin, J. A. Prescher, S. T. Laughlin, N. J. Agard, P. V. Chang, I. A. Miller, A. Lo, J. A. Codelli, and C. R. Bertozzi, Proc. Natl. Acad. Sci. USA, 2007, 16793. CrossRef
11. J.-F. Lutz, Angew. Chem. Int. Ed., 2007, 46, 1018. CrossRef
12. a) V. O. Rodionov, S. I. Presolski, S. Gardinier, Y.-H. Lim, and M. G. Finn, J. Am. Chem. Soc., 2007, 129, 12696; CrossRef b) V. O. Rodionov, S. I. Presolski, D. D. Díaz, V. V. Fokin, and M. G. Finn, J. Am. Chem. Soc., 2007, 129, 12705. CrossRef
13. a) C. Girard, E. Ӧnen, M. Aufort, S. Beauvière, E. Samson, and J. Herscovici, Org. Lett., 2006, 8, 1689; CrossRef b) A. Sarkar, T. Mukherjee, and S. Kapoor, J. Phys. Chem. C, 2008, 112, 3334. CrossRef
14. S. Chassaing, M. Kumarraja, A. S. S. Sido, P. Pale, and J. Sommer, Org. Lett., 2007, 9, 883. CrossRef
15. R. B. N. Baig and R. S. Varma, Green Chem., 2012, 14, 625. CrossRef
16. B. H. Lipshutz and B. R. Taft, Angew. Chem. Int. Ed., 2006, 45, 8235. CrossRef
17. a) D. Raut, K. Wankhede, V. Vaidya, S. Bhilare, N. Darwatkar, A. Deorukhkar, G. Trivedi, and M. Salunkhe, Catal. Commun., 2009, 10, 1240; CrossRef b) J. C. Park, A. Y. Kim, J. Y. Kim, S. Park, K. H. Park, and H. Song, Chem. Comm., 2012, 48, 8484; CrossRef c) G. Molteni, C. L. Bianchi, G. Marinoni, N. Santo, and A. Ponti, New J. Chem., 2006, 30, 1137; CrossRef d) L. D. Pachón, J. H. van Maarseveen, and G. Rothenberg, Adv. Synth. Catal., 2005, 347, 811; CrossRef e) E. D. Pressly, R. J. Amir, and C. J. Hawker, J. Polym. Sci. Part A: Polym. Chem., 2011, 49, 814. CrossRef
18. a) P. Appukkuttan, W. Dehaen, V. V. Fokin, and E. Van der Eycken, Org. Lett., 2004, 6, 4223; CrossRef b) P. Cintas, A. Barge, S. Tagliapietra, L. Boffa, and G. Cravotto, Nat. Protoc., 2010, 5, 607. CrossRef
19. J. Y. Kim, J. C. Park, H. Kang, H. Song, and K. H. Park, Chem. Commun., 2010, 46, 439. CrossRef
20. R. Hudson, C.-J. Li, and A. Moores, Green Chem., 2012, 14, 622. CrossRef
21. General protocol; To a stirred solution of benzyl azide (1.0 mmol), phenylacetylene (1.5 mmol) and triethylamine (1.0 mmol) in ethyl acetate (2.0 mL) were added nano-CuFe2O4 powder (0.05 mmol) and 2,2’-bipyridine (0.05 mmol). The reaction mixture was stirred at room temperature for 24 h. After completion of the reaction, the reaction mixture was extracted with ethyl acetate (2 mL x5). The combined solution was concentrated in vacuo to give the crude product, which was washed with hexane (10 mL x2) and then purified by flash column chromatography (H:EA = 5:1) on silica gel to yield the product as a white solid.
Recycling Experiment for CuFe2O4 Nanoparticles; After completion of the reaction, the catalyst was recovered magnetically with the aid of an external magnet, and washed with ethyl acetate. It was directly used or dried under reduced pressure.
22. K. Namitharan, M. Kumarraja, and K. Pitchumani, Chem. Eur. J. 2009, 15, 2755. CrossRef