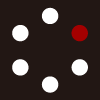
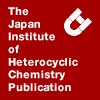
HETEROCYCLES
An International Journal for Reviews and Communications in Heterocyclic ChemistryWeb Edition ISSN: 1881-0942
Published online by The Japan Institute of Heterocyclic Chemistry
e-Journal
Full Text HTML
Received, 7th August, 2009, Accepted, 18th September, 2009, Published online, 18th September, 2009.
DOI: 10.3987/COM-09-11814
■ Oxidant-Free Lactonization of Diols Using a Hydrotalcite-Supported Copper Catalyst
Yusuke Mikami, Kaori Ebata, Takato Mitsudome, Tomoo Mizugaki, Koichiro Jitsukawa, and Kiyotomi Kaneda*
Research Center for Solar Energy Chemistry, Graduate School of Engineering Science, Osaka University, 1-3 Machikaneyama, Toyonaka, Osaka 560-8531, Japan
Abstract
We newly synthesized well-crystallized hydrotalcite-supported copper nanoparticles, denoted as Cu/HT(c), which acted as a highly efficient heterogeneous catalyst for oxidant-free lactonization of various diols under liquid-phase conditions. The Cu/HT(c) catalyst could be recovered by simple filtration and reused without the significant loss of its activity and selectivity.Lactones are important as components of flavors, medicines, and solvents, and as synthetic intermediates for herbicides and rubbers.1 Among many approaches to the synthesis of lactones,2 the oxidant-free catalytic lactonization of diols is one of the most attractive protocols because of easy availability of diols, high atom efficiency, and production of only nonpolluting molecular hydrogen as a coproduct (Scheme 1).3 In particular, supported Cu-particle catalysts are economically attractive for the oxidant-free lactonization of diols.4 However, to date, such catalysts require high temperatures and the addition of hazardous chromium compounds to prevent the aggregation of Cu particles.
We have designed efficient heterogeneous catalysts based on the properties of hydrotalcites (HT; Mg6Al2(OH)16CO3・nH2O).5 Very recently, we found that Cu nanoparticles supported on HT (Cu/HT) showed high catalytic activity for the oxidant-free dehydrogenation of various alcohols into the corresponding carbonyl compounds.6 The Cu/HT catalyst was much more active than other heterogeneous Cu catalysts because Cu nanoparticles were highly stable on HT and did not aggregate into inactive Cu species.
To further investigate the catalytic potential of Cu/HT, herein we newly synthesized well-crystallized hydrotalcite-supported Cu nanoparticles, denoted as Cu/HT(c). These nanoparticles act as a highly efficient heterogeneous catalyst for the oxidant-free lactonization of various diols under liquid-phase conditions. The Cu/HT(c) catalyst overcomes problems previously reported for many Cu catalyst systems, such as the need for additional chromium compounds, high temperatures, and high catalyst loadings.4 The catalyst can be removed from the reaction mixture by simple filtration and reused without the loss of its activity and selectivity.
To synthesize Cu/HT(c), we upgraded the Cu/HT previously prepared6 by subsequent hydrothermal treatment of HT.7 The specifics are as follows: 70 mL of a mixed salt solution containing MgCl2 (21 mmol) and AlCl3 (7.0 mmol) was added quickly (within 5 s) to 280 mL of an aqueous NaOH solution (150 mM) under vigorous stirring, followed by stirring for 30 min under Ar atmosphere and subsequent separation by centrifugation. The resulting slurry was washed with deionized water (150 mL), dispersed in 100 mL of deionized water, and transferred to a Teflon-lined stainless-steel autoclave, which was placed in a preheated oven and treated hydrothermally at 100 °C for 16 h. The suspension was dried by evaporation to afford well-crystallized white solid HT(c) (1.2 g). The XRD measurement (Figure 1) showed the peak intensity of (003) to be 2.5 times greater than that reported previously for HT. Crystallite sizes of HT(c) and HT calculated with Scherrer’s equation were 19 and 16 nm, respectively. The obtained HT(c) (1.0 g) was added to 50 mL of an aqueous solution of Cu (II) trifluoromethanesulfonate (0.80 mmol). The mixture was stirred for 2 min, adjusted to a pH of 8.0 by the addition of an aqueous solution of ammonia (25%), further stirred for 1 h at 25 °C, and filtered, and the solid was washed with deionized water and dried. The resulting pale blue powder, HT(c)-supported Cu (II) species CuII/HT(c), was dried in vacuo at 180 °C and reduced with 1 atm of H2 to afford well-crystallized Cu/HT(c) (4.5 wt%). XRD measurement (Figure 1) shows the peak intensity of (003) to be 2.0 times greater than that reported previously for Cu/HT. TEM analysis (Figure 2) shows the mean Cu-nanoparticle diameter to be 6.1 nm (standard deviation 2.4 nm), indicating the formation of nanoparticles of uniform size. The size of these nanoparticles is smaller than those of our previous Cu/HT (mean diameter 7.5 nm, standard deviation 4.3 nm).
We applied the Cu/HT(c) catalyst to the model reaction of the lactonization of 1,4-butanediol (1). Under
Ar atmosphere, 1 (1.0 mmol) was added to mesitylene (5.0 mL) in the presence of Cu/HT(c) (0.10 g) and the mixture was stirred at 150 °C.8 After 3 h, 1 was completely converted to give γ-butyrolactone (2) in >99% yield together with two equivalents of molecular hydrogen; other products from 1 such as tetrahydrofuran, n-butanol, and γ-hydroxybutyraldehyde were not formed (Table 1, entry 1). After removal of the Cu/HT(c) catalyst from the reaction mixture at 50% conversion of 1, further stirring of the filtrate under similar conditions did not yield any products, and negligible amounts of Cu species (0.08% of the Cu species initially present) were detected in the filtrate by inductively coupled plasma (ICP) analysis. These results clearly show that lactonization occurs on the surface of Cu/HT(c).
Among the various supports containing Cu nanoparticles that we examined, Cu/HT(c) showed the highest catalytic activity (>99% yield of 2), and Cu/SiO2 showed excellent activity (95% yield of 2) (Table 1, entries 1 and 6). In contrast, Cu/Al2O3, Cu/TiO2, Cu/MgO, and Cu/HAP afforded much lower yields of 2 (Table 1, entries 8–11). Interestingly, the present Cu/HT(c) catalyst showed significantly higher activity than our previous Cu/HT; the latter, prepared by coprecipitation, afforded 64% yield of 2 (Table 1, entry 1 vs. entry 7). The difference in performance between Cu/HT(c) and Cu/HT may be due to the former’s smaller, uniform particle size, as discussed above. The solvent was also found to affect yield significantly. Mesitylene afforded excellent yield of 2, whereas DMA and DMSO did not (Table 1, entries 1, 4, and 5).
The scope of Cu/HT(c) for the lactonization of a wide range of diols is shown in Table 2. Various diols were oxidized to afford the corresponding lactones in high yields; aliphatic diols and a diol containing an aromatic group were sufficiently converted to lactones (Table 2, entries 1–8). 1,4-Pentanediol selectively yielded γ-valerolactone (Table 2, entry 2),9 indicating that a primary hydroxyl function of 1,4-pentanediol
preferentially oxidizes to hydroxyaldehyde, which is in equilibrium with alactol, and subsequent oxidation of the lactol yields the corresponding γ-valerolactone. Furthermore, the Cu/HT(c) catalyst effectively catalyzes reaction of a nitrogen-containing diol of N-methyldiethanolamine to afford the corresponding product 4-methyl-2-morpholinone in quantitative yield (Table 2, entry 9).
The Cu/HT(c) catalyst was applicable successfully for the scale-up conditions. Dehydrogenation of 1 (3.6 g) at a 40-mmol scale afforded 95% isolated yield of 2 (3.3 g) in which the turnover number (TON) reached 531. The value of TON is higher than those reported for other heterogeneous Cu catalysts such as Cu–Zn–Ru (TON = 107),4d CuO–Cr2O3–BaO (TON = 38),4i and CuCr2O4 (TON = 47 and 60).4j,4k
Moreover, the Cu/HT(c) catalyst proved to be recyclable for dehydrogenation of 1, with similar reaction rates (Table 1, entries 2 and 3). TEM analysis shows that the average Cu-nanoparticle diameter for the reused catalyst is similar to that for the fresh catalyst, and there is no apparent aggregation, suggesting good durability for recycling.
In conclusion, we found that Cu nanoparticles supported on well-crystallized HT (Cu/HT(c)) are highly active heterogeneous catalysts for the lactonization of diols under liquid-phase conditions. The Cu/HT(c) catalyst exhibits high activity and wide applicability for various diols without the need of oxidants or chromium compounds. The catalyst is reusable, is highly resistant to aggregation of Cu particles, and is applicable to scale-up.
ACKNOWLEDGEMENTS
This investigation was supported by a Grant-in-Aid for Scientific Research from the Ministry of Education, Culture, Sports, Science, and Technology of Japan. This work was also supported by a Grant-in-Aid for Scientific Research on Priority Areas (No.18065016, "Chemistry of Concerto Catalysis") from the Ministry of Education, Culture, Sports, Science, and Technology, Japan. Some experiments were carried out using the facilities at the Research Center for Ultrahigh Voltage Electron Microscopy, Osaka University. One of the authors Y.M. thanks the JSPS Research Fellowships for Young Scientists. Y. M. express his special thanks for The Global COE (center of excellence) Program “Global Education and Research Center for Bio-Environmental Chemistry” of Osaka University.
References
1. A. Parenty, X. Moreau, and J.-M. Campagne, Chem. Rev., 2006, 106, 911. CrossRef
2. (a) M. Fetizon, M. Golfier, and J. M. Louis, Chem. Commun., 1969, 1118; CrossRef (b) M. Fetizon, M. Golfier, and J. M. Louis, Tetrahedron, 1975, 31, 171; CrossRef (c) V. I. Stenberg and R. J. Perkins, J. Org. Chem., 1963, 28, 323; CrossRef (d) P. Johnton, R. C. Sheppard, C. E. Stehr, and S. Turner, J. Chem. Soc. (C), 1966, 1847; CrossRef (e) M. Ito, A. Osaku, A. Shiibashi, and T. Ikariya, Org. Lett., 2007, 9, 1821; CrossRef (f) K. Nozaki, M. Yoshida, and H. Takaya, J. Organomet. Chem., 1994, 473, 253; CrossRef (g) Y. Shvo, Y. Blum, D. Reshef, and M. Menzin, J. Organomet. Chem., 1982, 226, C21; CrossRef (h) Y. Ishii, K. Osakada, T. Ikariya, M. Saburi, and S. Yoshikawa, J. Org. Chem., 1986, 51, 2034; CrossRef (i) Y. Ishii, K. Osakada, T. Ikariya, M. Saburi, and S. Yoshikawa, Chem. Lett., 1982, 1179; CrossRef (j) S. Murahashi, T. Naota, K. Ito, Y. Maeda, and H. Taki, J. Org. Chem., 1987, 52, 4319; CrossRef (k) S. Murahashi, K. Ito, T. Naota, and Y. Maeda, Tetrahedron Lett., 1981, 22, 5327; CrossRef (l) Y. Lin, X. Zhu, and Y. Zhou, J. Organomet. Chem., 1992, 429, 269; CrossRef (m) H. C. Maytum, B. Tayassoli, and J. M. J. Williams, Org. Lett., 2007, 9, 4387; CrossRef (n) Y. Ishii, K. Suzuki, T. Ikariya, M. Saburi, and S. Yoshikawa, J. Org. Chem., 1986, 51, 2822; CrossRef (o) Y. Tamaru, Y. Yamada, K. Inoue, Y. Yamamoto, and Z. Yoshida, J. Org. Chem., 1983, 48, 1286; CrossRef (p) I. Minami and J. Tsuji, Tetrahedron, 1987, 43, 3903; CrossRef (q) T. Suzuki, K. Morita, M. Tsuchida, and K. Hiroi, Org. Lett., 2002, 4, 2361. CrossRef
3. J. Zhao and J. F. Hartwig, Organometallics, 2005, 24, 2441. CrossRef
4. (a) Y. L. Zhu, J. Yang, G. Q. Dong, H. Y. Zheng, H. H. Zhang, H. W. Xiang, and Y. W. Li, Appl. Catal. B, 2005, 57, 183; CrossRef (b) N. Ichikawa, S. Sato, R. Takahashi, T. Sodesawa, and K. Inui, J. Mol. Catal. A, 2004, 212, 197; CrossRef (c) R. Fischer and R. Pinkos, Jap. Pat., 2003, JP 2003-508392; (d) Y. Abe, H. Imoto, and K. Gaiya, Jap. Pat., 1992, JP 4-261167; (e) H. Koyama, Jap. Pat., 1990, JP 2-255668; (f) S. Oka, Bull. Chem. Soc. Jpn., 1961, 34, 12; CrossRef Additional chromium compounds: (g) R. Sigg, H. Regner, Jap. Pat., 1995, JP 7-10859; (h) T. Ichiki, K. Kobayashi, and S. Suzuki, Jap. Pat., 1994, JP 6-73042; (i) H. E. Bellis, US Pat., 1992, US 5110954; (j) R. K. Summerbell, D. M. Jerina, and R. J. Grula, J. Org. Chem., 1962, 27, 4433; CrossRef (k) L. E. Schniepp and H. H. Geller, J. Am. Chem. Soc., 1947, 69, 1545. CrossRef
5. (a) T. Mitsudome, Y. Mikami, H. Funai, T. Mizugaki, K. Jitsukawa, and K. Kaneda, Angew. Chem. Int. Ed., 2008, 47, 138; CrossRef (b) K. Mori, T. Mizugaki, K. Ebitani, and K. Kaneda, Bull. Chem. Soc. Jpn., 2006, 79, 981; CrossRef (c) K. Motokura, N. Fujita, K. Mori, T. Mizugaki, K. Ebitani, K. Jitsukawa, and K. Kaneda, Chem. Eur. J., 2006, 12, 8228; CrossRef (d) K. Yamaguchi, K. Mori, T. Mizugaki, K. Ebitani, and K. Kaneda, J. Org. Chem., 2000, 65, 6897. CrossRef
6. T. Mitsudome, Y. Mikami, K. Ebata, T. Mizugaki, K. Jitsukawa, and K. Kaneda, Chem. Commun., 2008, 4804. CrossRef
7. Z. Xu, G. Stevenson, C. Liu, and G. Q. (M.) Lu, J. Phys. Chem. B, 2006, 110, 16923. CrossRef
8. The reaction procedure is as follows: Cu/HT(c) (0.10 g, Cu: 0.071 mmol) was placed in a reaction vessel equipped with a reflux condenser topped with a mineral oil bubbler. Mesitylene (5.0 mL) and 1,4-butanediol (1.0 mmol) were added, and the reaction mixture was vigorously stirred at 150 °C under Ar flow for 3 h. The solid catalyst was removed by centrifugation and the yield was determined by GC analysis with naphthalene as an internal standard. The amount of generated hydrogen is measured by gas burette attached to the reactor.
9. This high selectivity for formation of γ-valerolactone is comparable to previous reported systems using precious metal catalysts with acetone or O2 as hydrogen acceptors.2e,2j,2q,10.
10. (a) S. Kobayashi, H. Miyamura, R. Akiyama, and T. Ishida, J. Am. Chem. Soc., 2005, 127, 9251; CrossRef (b) K. Ebitani, H.-B. Ji, T. Mizugaki, and K. Kaneda, J. Mol. Catal. A, 2004, 212, 161. CrossRef